Bosch Indego robotic lawn mower - tips and tricks
At the time of this post’s writing, I’ve had my Bosch Indego robotic lawn mower for seven seasons and it’s still happily taking care of my lawn. I admit it has been through more services, software updates and repairs than I expected but so far Bosch and my reseller has been very understanding and every single case has been covered by warranty and/or paid in full by Bosch. I’ve learned a thing or two about this robot over the years, both through Bosch support and my own findings, and thought I’d share some tips and tricks.
Just to clarify, this post refers to the first generation robotic lawn mower (Indego 800 - 1200) and not the newer Connect series.
Important note
If you suspect something is wrong with your device, always contact Bosch support first. Modifying and replacing parts yourself is done at your own risk.
Some of the instructions in this post may void the warrany of your unit, damage it and make it less safe to operate. Even if something helped me, it may not help you. You have been warned, use at your own risk.
Table of contents
Overview
The first generation Bosch Indego has a couple of years behind it. As such, it may be a bit bigger and louder than current generation units. But as I see it, it still has one big advantage - something called Logicut. This robot learns the boundaries of your lawn and keeps an internal map of it. Once learned, the robot knows exactly where it has and has not been and will resume at the exact spot it left after charging the battery. Logicut also makes the robot work in straight, parallell lines (like traditional mowing) instead of randomly bouncing around. This means it’s much easier to plan ahead and move back garden toys, grills, etc, when the robot is finished with an area - because it won’t return to the same spot twice in the same run (except maybe for a pass through).
Logicut (left), random cutting (right).
Wheel tracks
The Indego will most likely leave at least some wheel tracks on your lawn. Especially during the learning phase (the two first complete runs of the lawn) it re-uses the same paths extensively as it navigates on top of the perimeter wire. Unfortunately there is no variation or offset from the wire, so the Indego will use the exact same tracks every time. (This could have been easily fixed by introducing a small offset/randomness in how it positions with regards to the perimeter wire position, varying for every run.) Some other factors contributing to visible wheel tracks are the weight of the Indego and the fact that the driving wheels are not ribbed enough. Obviously the running time and schedule is a big factor as well.
After the learning phase the Indego will start to navigate more without help of the perimeter wire, ideally only using it for a short distance before the docking station or when edge cutting is scheduled. The wheel tracks typically won’t appear the first season and you can of course slightly adjust the perimeter wire between seasons to prevent it as much as possible. But it also depends a lot on your lawn. If you have a very dense and strong lawn, chances are wheel tracks won’t be visible. I have some areas of my lawn with very visible wheel tracks (where the grass is thin or no grass at all) and other places, where the Indego has not used the perimeter wire as much and also having denser grass, where it’s barely visible.
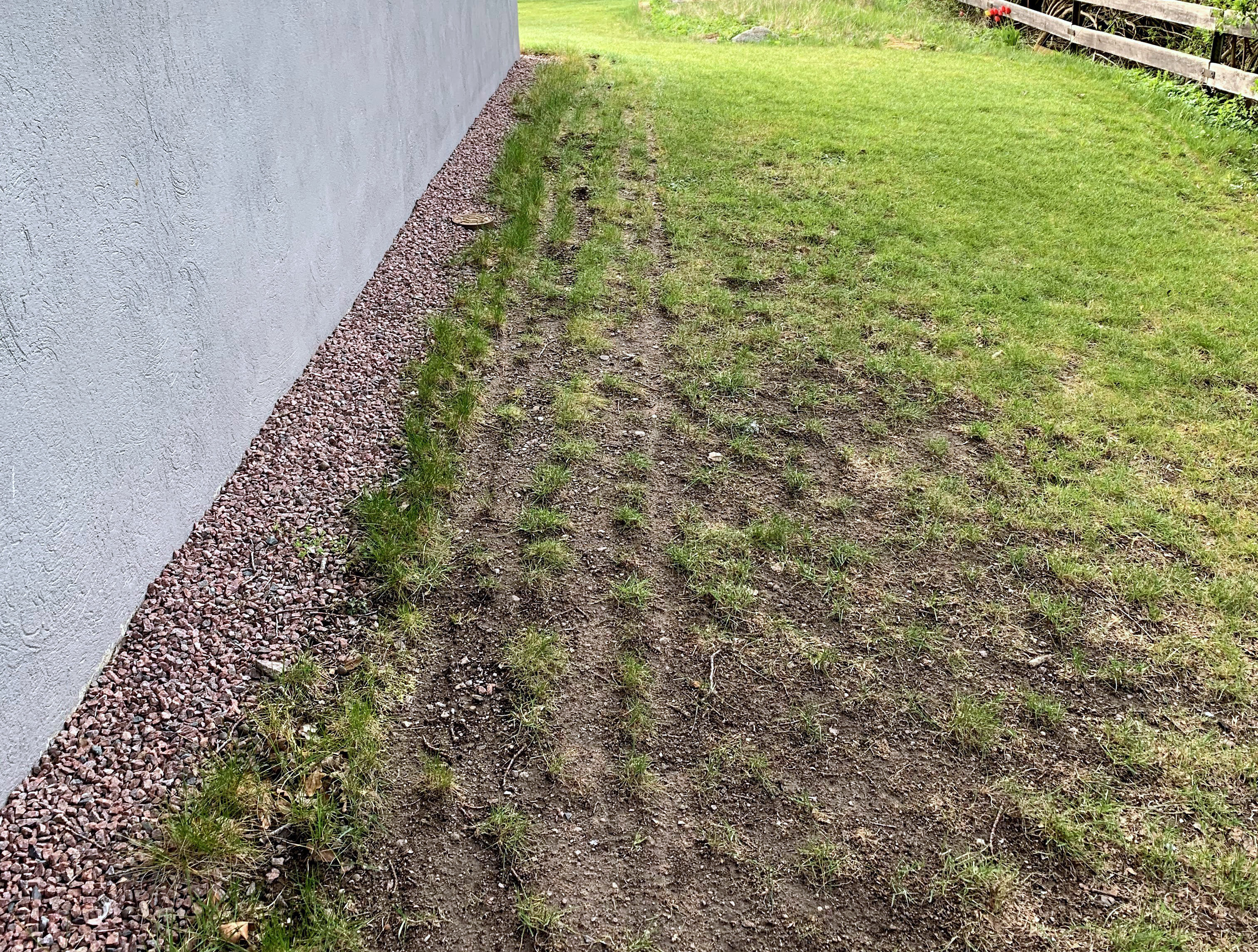
Visible wheel tracks will appear where the grass is too weak or missing.
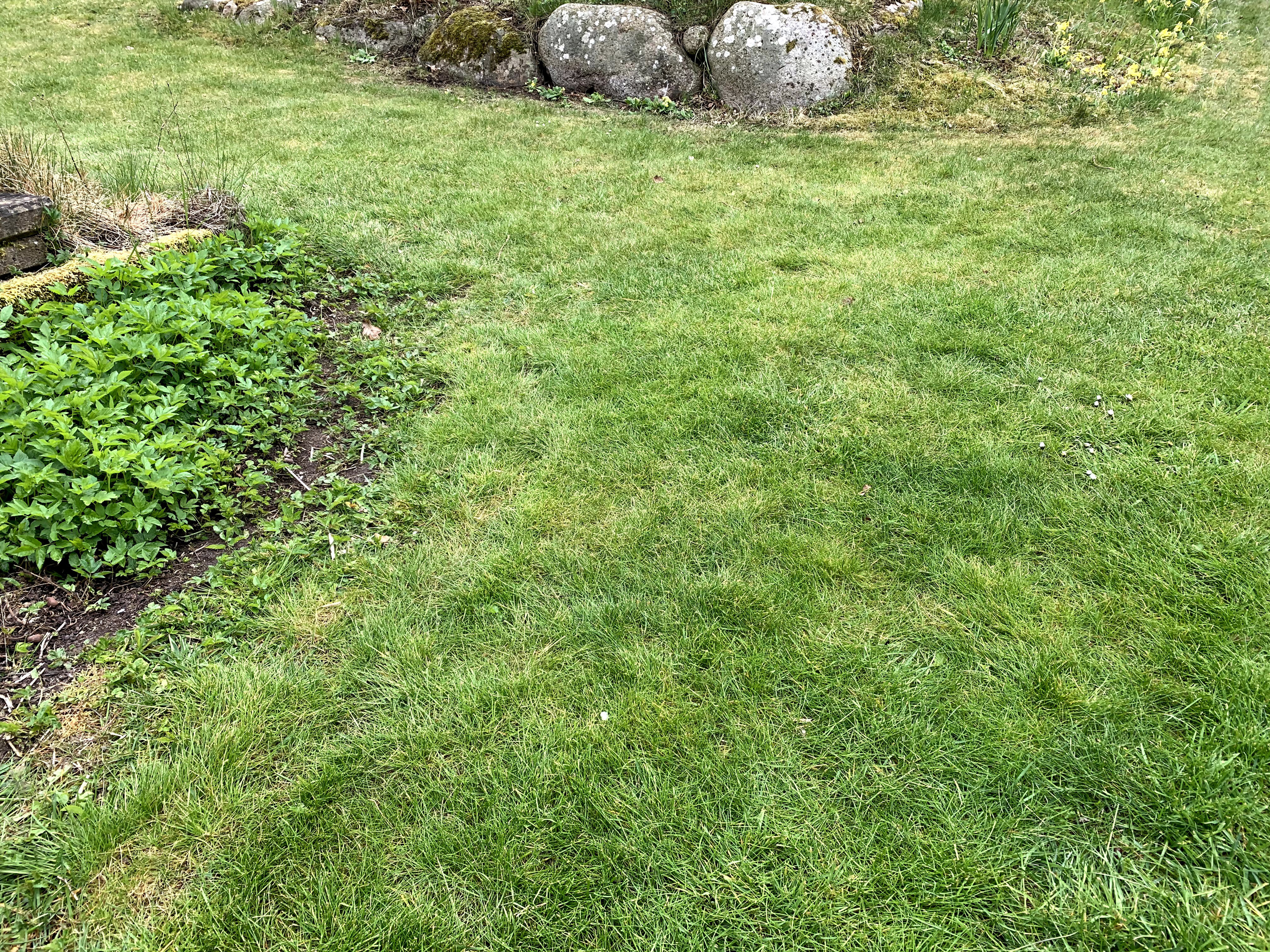
Less distinct wheel tracks due to denser grass.
Cutting height
I set my cutting height quite high, seven out of ten. The most common mistake for new robotic lawn mower owners is setting this too low, causing the grass to dry out easily and turn yellow. The lawn will still look groomed with a higher setting, since the Indego will make sure the grass is evenly cut. I suggest starting somewhat higher and lower it gradually until you’re happy; the cutting height is of course very dependant on the climate, grass type, etc.
Trimming edges
The Indego will not cut all the way out to the lawn edge. Smart positioning of the perimeter wire and the use of stone slabs around edges can minimize this, but you will still need to trim some areas manually.
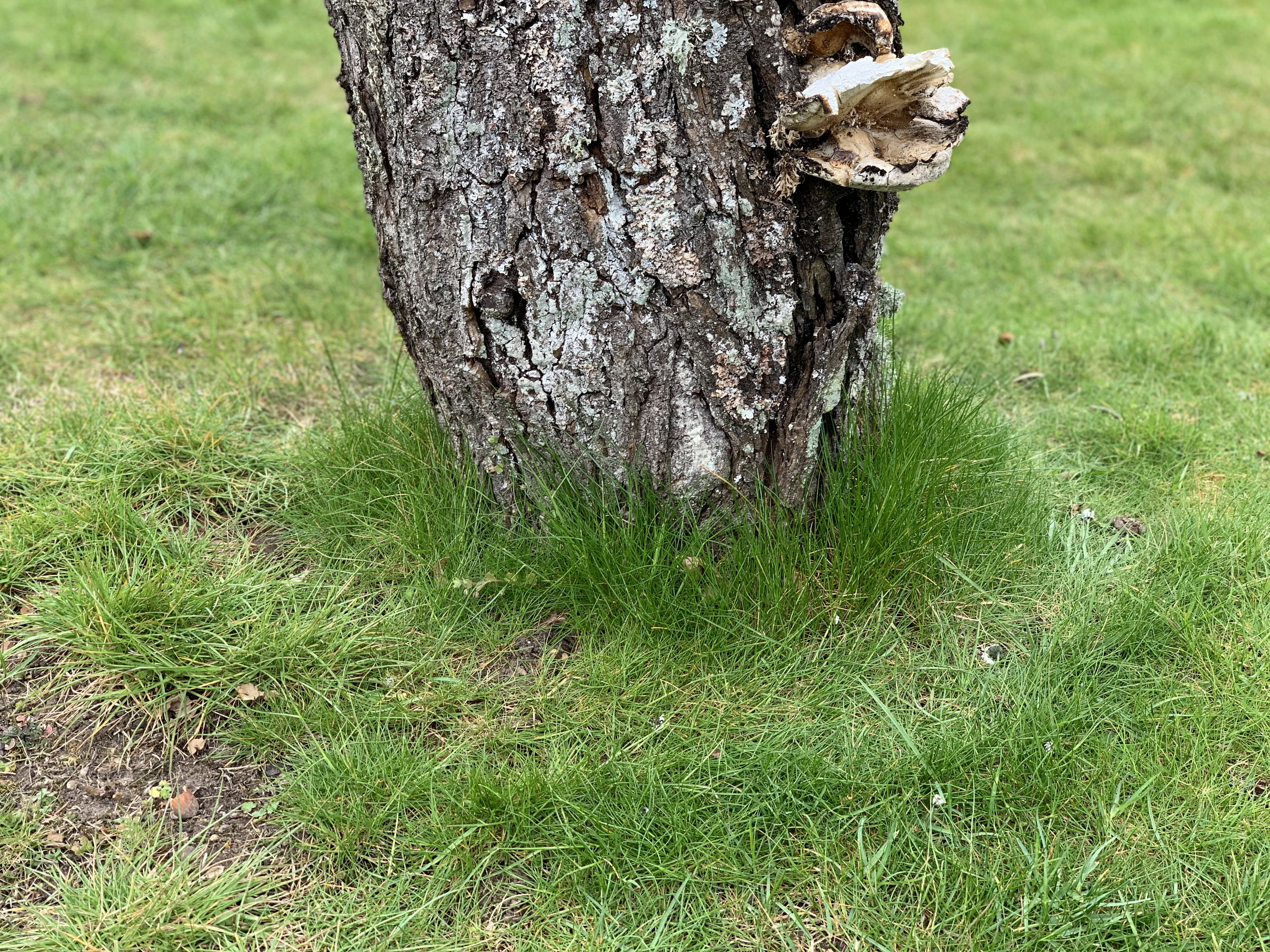
Manual trimming around trees is still needed.
Perimeter wire
Lawn size and wire length
I have the Indego 1000 model which is rated for lawns up to 1000 m2. My yard is actually 1600 m2, although not all of it is grass. Once fully learned, the Indego covers this area in about ten hours.
At this time I think I put down around 5-600 meters perimeter wire in total. This is more than the manual suggest but it does not cause any problems.
Pegging or digging?
The perimeter wire can be buried fairly deep without losing the signal (I have it down 5-6 cm at places, below stone slabs). For the first season I would recommend to keep the wire on top of the lawn, pegged down with the included pegs. After observing the robot for a few weeks you will most likely notice some problematic areas or places where you want to adjust the wire closer to a tree/bush etc. Keeping it on top of the lawn until all such adjustments have been made saves a lot of time.
Once you’re happy with the wire positioning, you can go ahead and dig it down if you want to. It’s a lot of work (especially for a big lawn) but it will prevent you from accidently ripping up the wire when raking leaves.
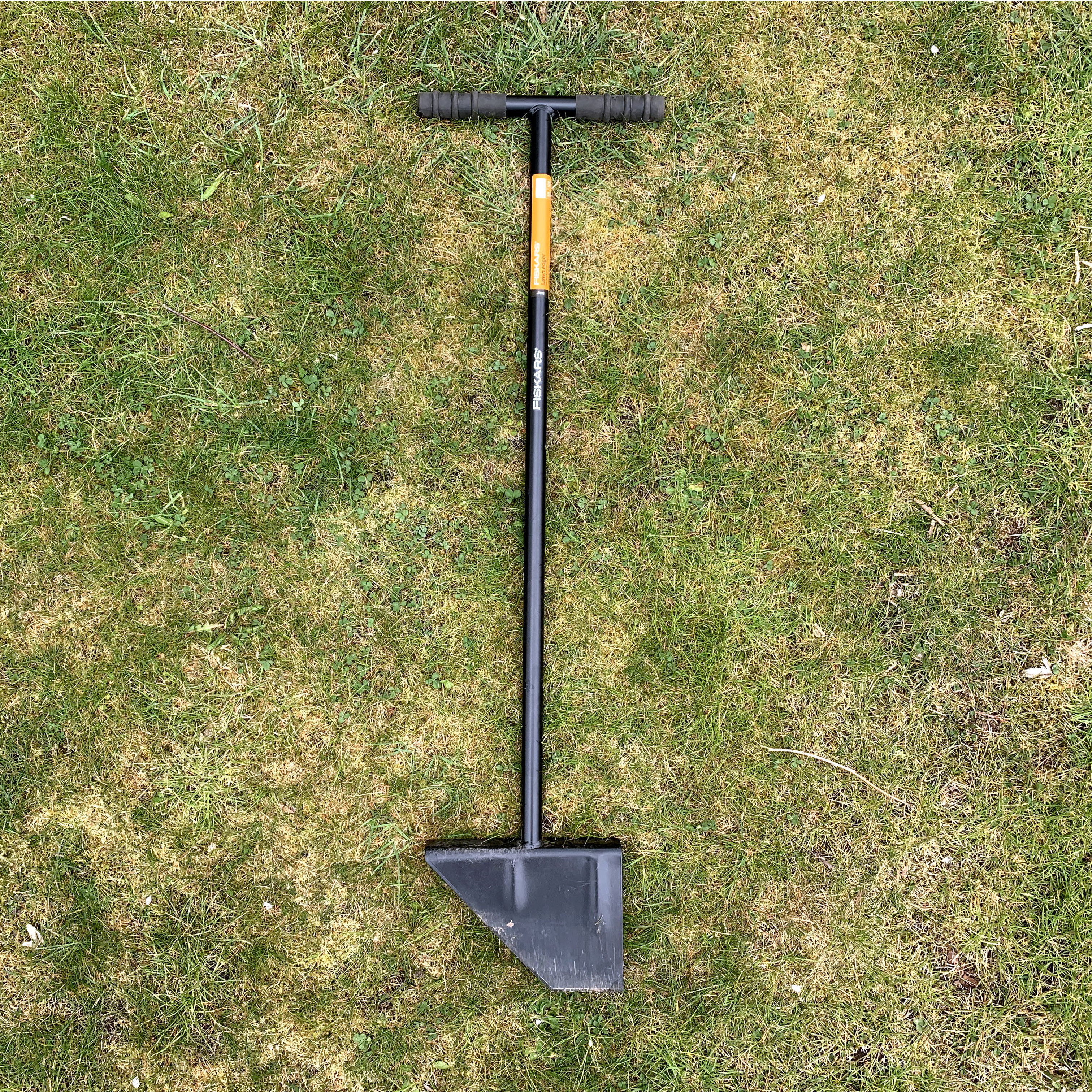
The first seasons I crawled on my knees and manually dug down the wire with a garden trowel, now I use a lawn edger.
Re-map after modifications!
The Indego is really sensitive when it comes to adjusting the perimeter wire. Always reset and re-map when making changes. With a long perimeter wire it can get confused with adjustments as small as a couple of centimeters. Keep in mind a reset means the unit will need to spend some time to re-learn your lawn, so it’s best to note down and bundle multiple wire changes together in one go.
Cable tracker
A cable tracker is a really helpful tool for finding problems with the perimeter wire and connectors. Always use good quality cable, like the one included with the Indego, to keep the cable functional over many years. Still, tree roots, ground going from frozen to thawed, driving heavy vehicles on the lawn, etc, can all cause the wire to move or break. A wire testing tool will help in finding the exact location of the cut - just connect it to the start of the cable (at the docking station) and walk along the wire with the hand held part to find where the signal goes weak.
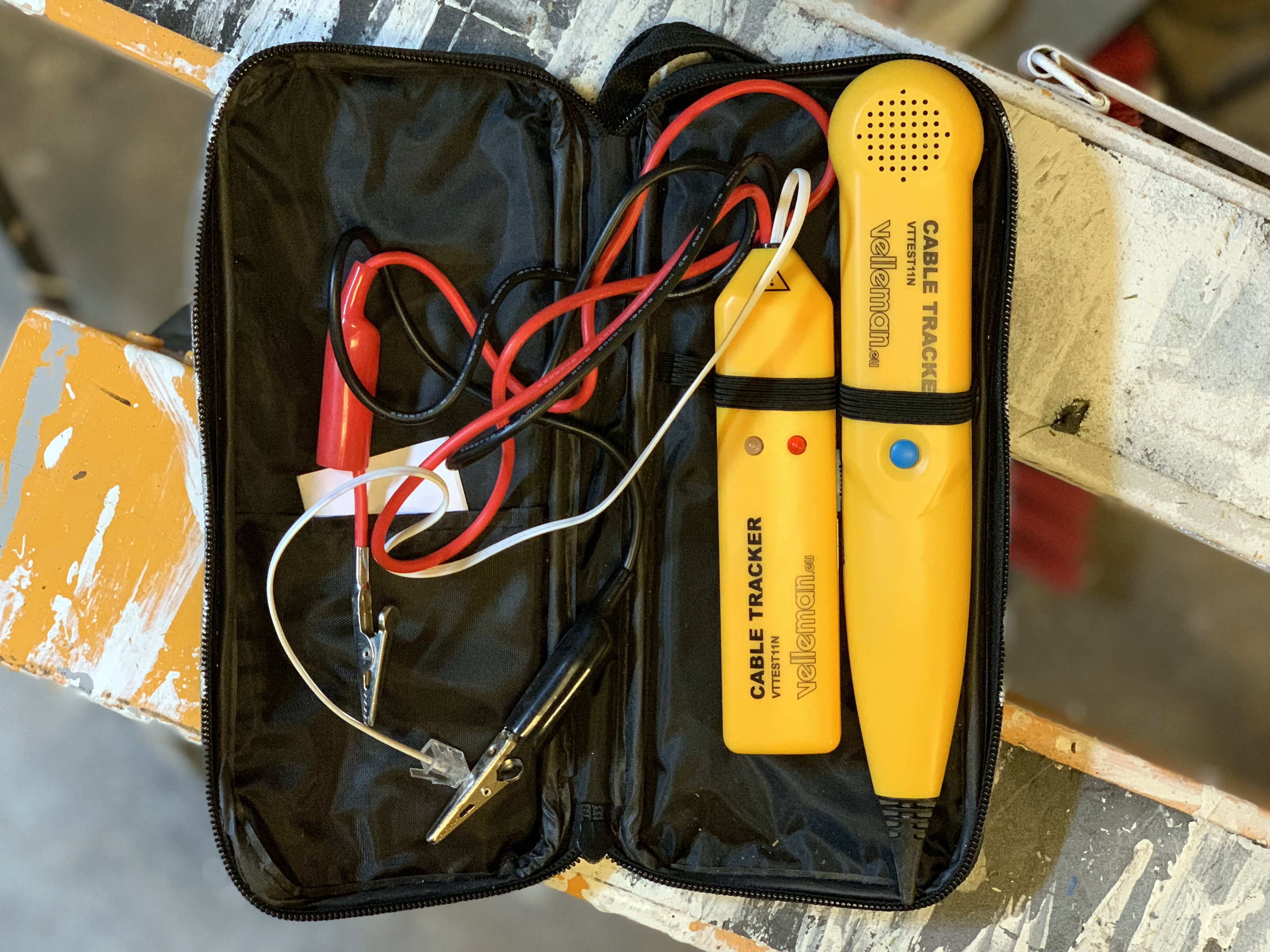
A cable tracker is helpful for finding weak connections or cuts in the perimeter wire.
Housing
While the Indego is marketed as rain proof, I would highly recommend to build some sort of housing or roof for it. After one of the bigger services my device went through I got a note back explaining water had reached some of the internal electronics and damaged multiple components, and a recommendation from the service team to keep it protected from rain. This was a very rainy summer. Remember, this device (at least mine) stays outdoors from spring to autumn, 24/7. You can of course move it in and out according to the weather if you want to, but building a simple house or roof is not that hard. Just remember to keep the entrance and inner side of the docking station clear so the Indego can dock and move out freely.
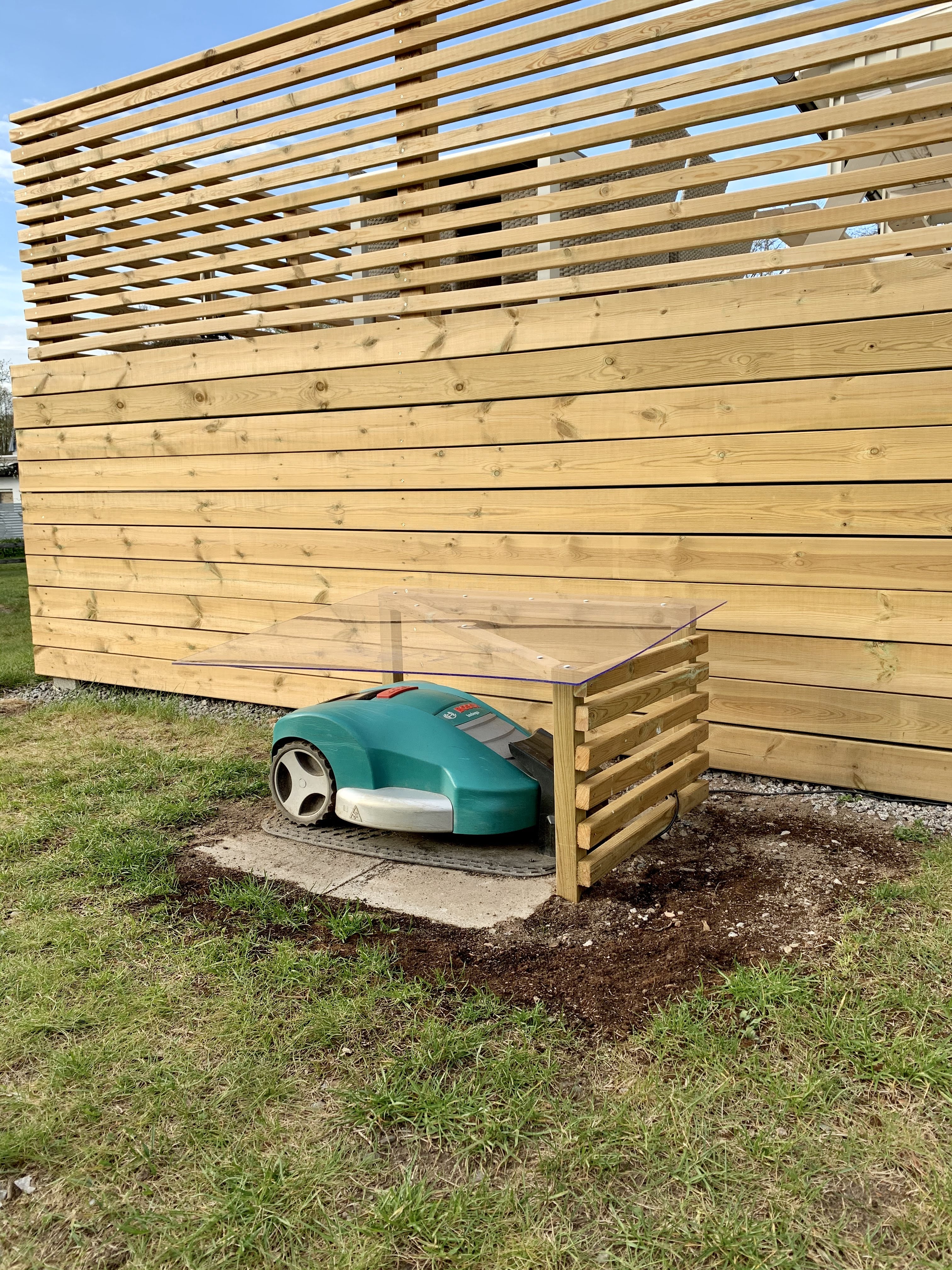
A simple transparent plastic roof protects from rain.
Lift sensors
The Indego is equipped with several sensors for identifying lifts and tilts, causing the device to stop. Two of these lift sensors are located at the front wheel bases. The sensors are essentially reed switches, causing the sensor to trigger when the wheel axles are fully extended (indicating the front of the unit has been lifted up from the ground). There is a cylindrical magnet in a plastic enclosure at the base of each wheel axle that moves away from the sensor, causing the reed switch to open (or close) and trigger the sensor.
Adjusting sensitivity of the lift sensors
Although not recommended, it is possible to adjust the sensitivity of the lift sensors to be more forgiving. This can be done by removing the wheel lift and slightly lifting the cylindrical magnet in the plastic enclosure upwards, so it gets closer to the reed switch, and fastening it so it won’t fall down to the original position. This adjustment must be done in very small steps and some trial and error is involved - lifting the magnet too far up disables the lift sensors completely, which is very dangerous as the cutting disc will keep rotating even when you lift it. Most of the time adjusting the magnets should not be needed. Only experiment with this on a spare set of front wheels and only as a last resort, e.g. if your lawn is too uneven and falsely triggers the lift sensors.
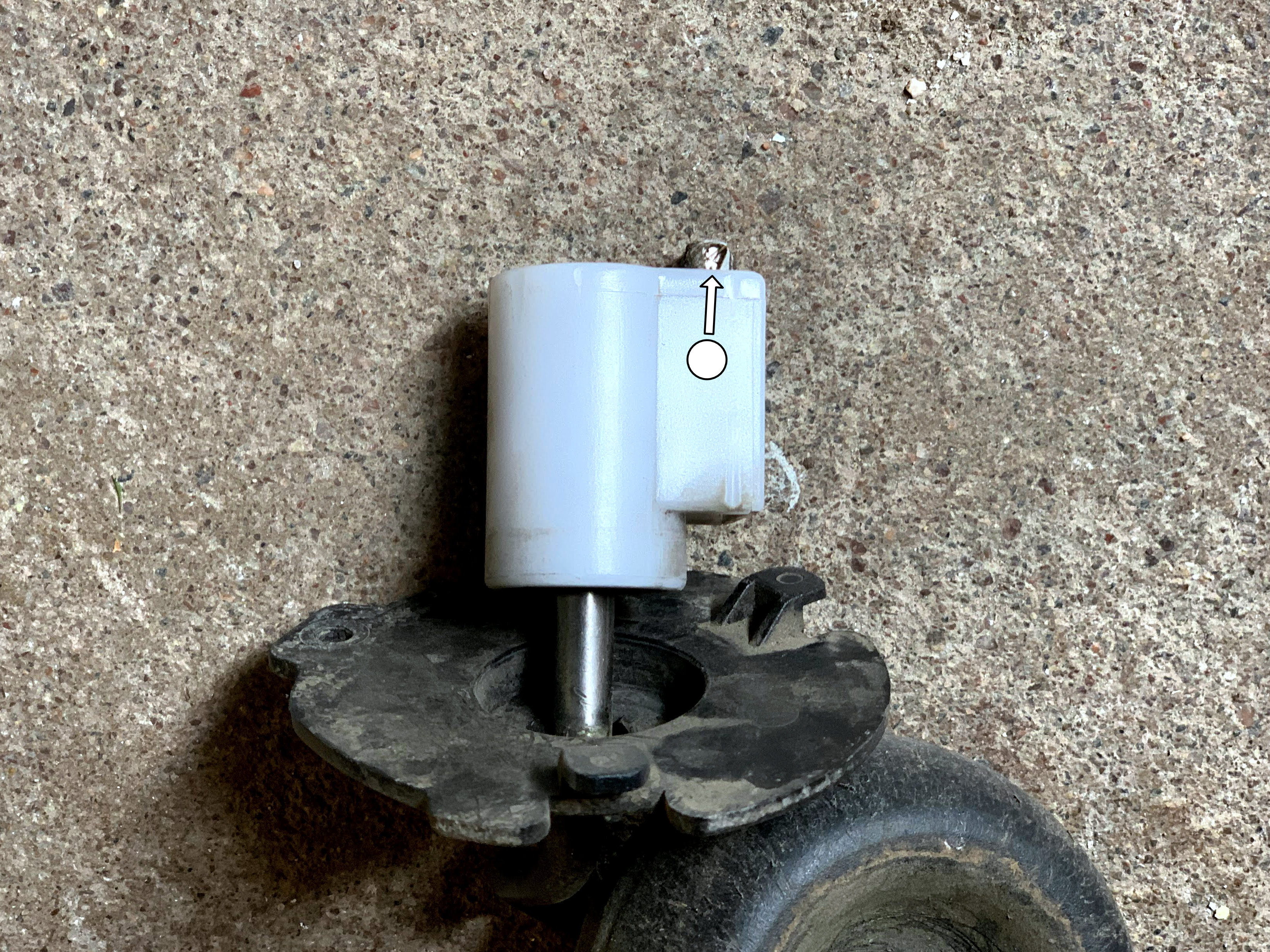
Raising the front wheel magnet from the original position (white circle) will reduce the lift sensor sensitivity (Note: use with caution)
Docking station
If there is one place where you should be particularly careful to get the perimeter wire straight and well within the bounds of the instruction manual, it’s at the docking station. If the wire does not go straight through the docking station, and keeps straight about two meters before and after, the Indego will probably have problems docking. Make sure to get this right from the start, double check the first couple of days that the Indego docks 100% of the time. It should never miss the charging pins. If it’s still missing the charging pins with a straight cable before, through and after, it could be a problem with “front wheel wobble”.
Front wheel wobble
The holes for the front wheel axles are, in my opinion, a quite poor design from Bosch. This area is subject to constant friction and tear. As the Indego moves around, the front wheel axles will move up and down pretty much constantly. The plastic in this area is very thin and the metal axles will eventually grind up the holes, causing a lot of sideways wobbling of the front wheels. This doesn’t cause any real issues out on the lawn, but eventually the wobbling will be large enough to cause the Indego to miss the charging pins when docking.
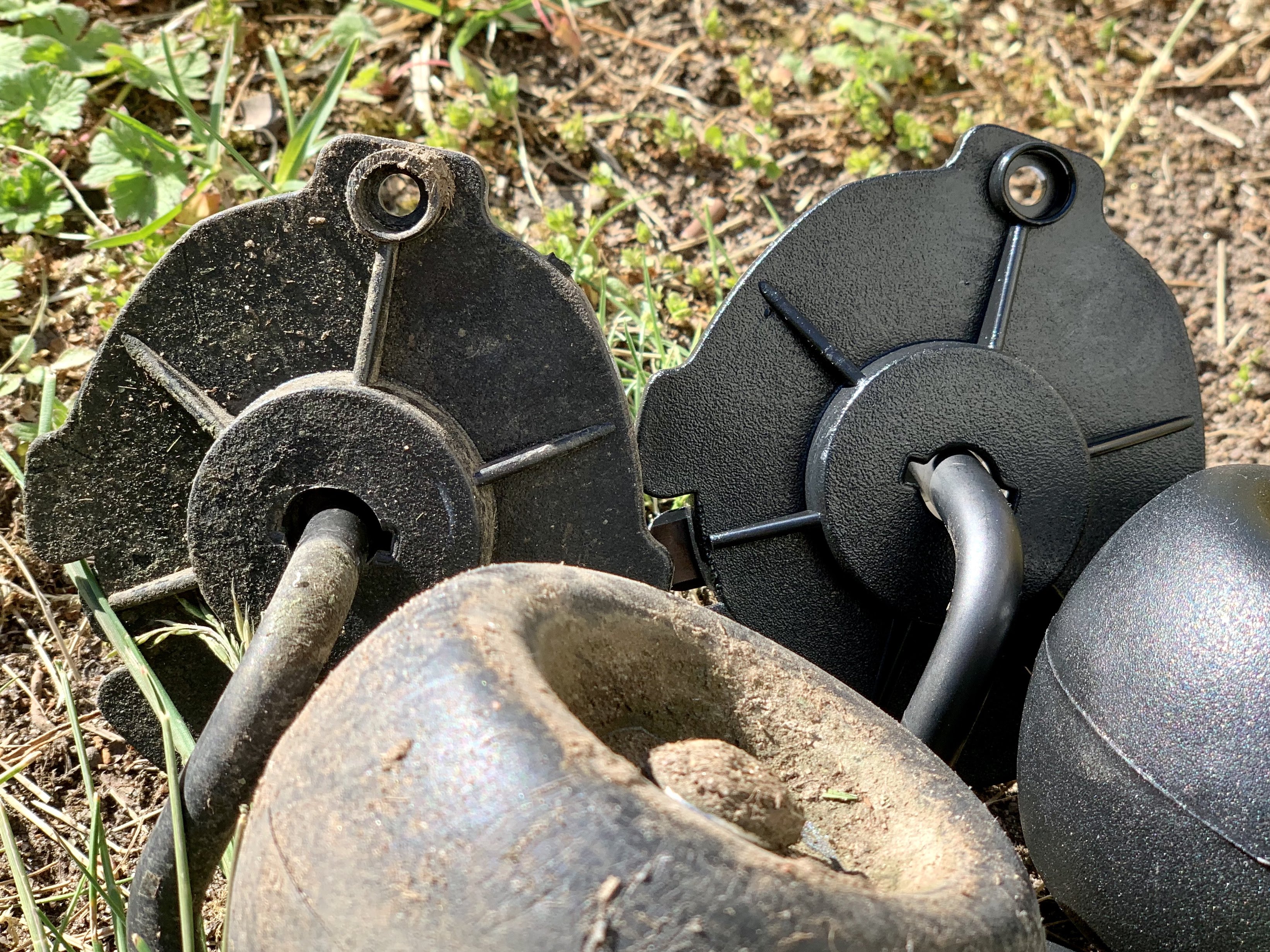
Worn out wheel axle hole (left) compared to a new one (right).
The wheel lift is a widely available spare part, very easy to remove (a single screw) and a new set of two complete front wheel lifts is about 50€ so it’s not that big deal to replace after a few seasons, but I think the plastic could have been strengthened a bit in this area. (This can of course be fixed with some creative DIY) Keeping the axles clean from sand and dirt and applying some dry lube from time to time will extend the lifetime, but next to the cutting blades this is probably what will wear out the fastest. Do NOT spray the wheel axles with liquid lube like WD-40. It will find its way down through the wheel housing into the reed switches below (lift sensors) and destroy them, rendering the device unusable (been there, done that). Only use a small amount of dry lube and let it dry completely before re-attaching the wheel lift.
Conclusion
In my case, having a robotic lawn mower has been really good for the lawn. Before, my lawn was spotty, irregular and had lots of weed and moss. Keeping the lawn constantly cut and regularely “feeding” it with small amounts of grass cuttings (both an effect of the robotic lawn mower) has definitely made my lawn denser and reduces blank spots. It has a lot less weeds in it but unfortunately it does not remove all of the moss, it’s not as much as before but it’s still there. As an added bonus, I can use the time previously spent on mowing the lawn with my kids or some other hobby. Or just grab a beer, sit down and watch the robot drive around.
I hope you found this post useful. Reach out on Twitter for leaving feedback and comments!